Like much of the country, the Boston area experienced a post-pandemic boom in demand for industrial facilities to serve the upward-trending e-commerce industry. According to CoStar, in 2023 the Boston area added 4 million square feet (SF) of new warehouse space, which was the most since 2001. The 2024 forecast is nearly 7 million SF which would be another new record for the market. Along with the demand for warehouse space came the demand for property that could support its development. Typically, warehouse and logistic space developers prefer large, flat land areas close to major transportation routes to build these expansive facilities. However, flat tracts of land that can accommodate the size of these facilities can be incredibly difficult to come by in the Boston area, which leaves developers turning to properties that require more extensive sitework to meet their facility needs.
Retaining walls can play a crucial role for addressing sitework obstacles, and retaining wall design requires careful planning and specialized geotechnical expertise. This article explores best practices in retaining wall design for warehouse and logistics buildings and highlights the value of early problem detection through geotechnical due-diligence and design.
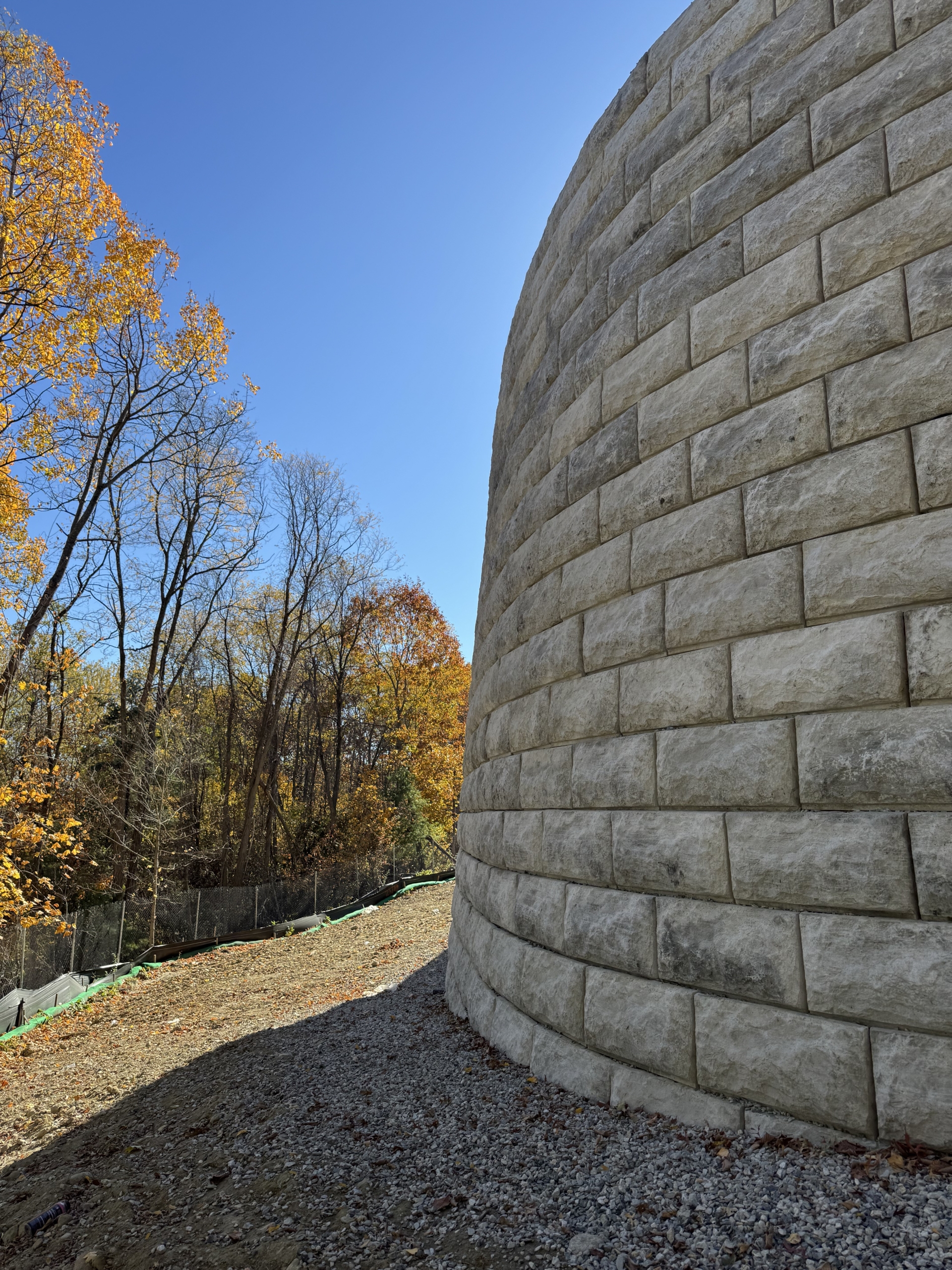
Tall Retaining Walls in Industrial Settings: Purpose and Demands
In warehouse and logistics applications, retaining walls are frequently needed to:
- Maximize usable space: Retaining walls allow developers to make the most of their property footprint, particularly in locations with uneven or extreme topography, which is crucial in densely developed or geographically constrained areas.
- Withstand heavy loads: In addition to lateral loading from earth pressures, loading from equipment, machinery, vehicles, and storage material are common considerations for retaining wall use in industrial settings.
To meet these demands, retaining walls used for industrial sites often exceed typical wall heights and lengths, reaching heights of more than 30 feet and stretching for thousands of feet in length (see photo 1 for an example). Traditionally, retaining wall design is completed by a design-build contractor and reviewed by a geotechnical engineer. These larger walls demand enhanced stability considerations, thorough soil analysis, and detailed geotechnical engineering to prevent issues like sliding, overturning, or structural failure–analyses not typically performed by design-build contractors.
Key Geotechnical Challenges for Tall Retaining Walls
Building tall retaining walls requires additional considerations in their planning and design:
- Construction phase conditions: Larger walls take more time to install and are subject to a wide variety of weather and construction variables. Wall design should consider interim and/or temporary conditions as well as the permanent construction condition which may take many months to achieve.
- Coordination with site layout: The influence of tall walls extends further into the site, and often intersects with building foundations loads, underground utilities, and stormwater management infrastructure. These elements of the site design need to be considered by the retaining wall designer.
- Site soil and groundwater conditions: Soil and groundwater conditions play a crucial role in considering design parameters for lateral pressures and foundation bearing capacity. Larger walls are more likely to support varying soil conditions, requiring additional design consideration, such as differential settlement. Additionally, soil conditions will influence the cut/fill balance at a site.
- Drainage and hydrostatic pressure mitigation: Groundwater and stormwater infiltration poses a significant risk to retaining wall stability for large retaining walls if a wall isn’t designed to resist hydrostatic pressure. The porosity and drainage capability of soils being retained by the wall also must be evaluated to limit hydrostatic pressure.
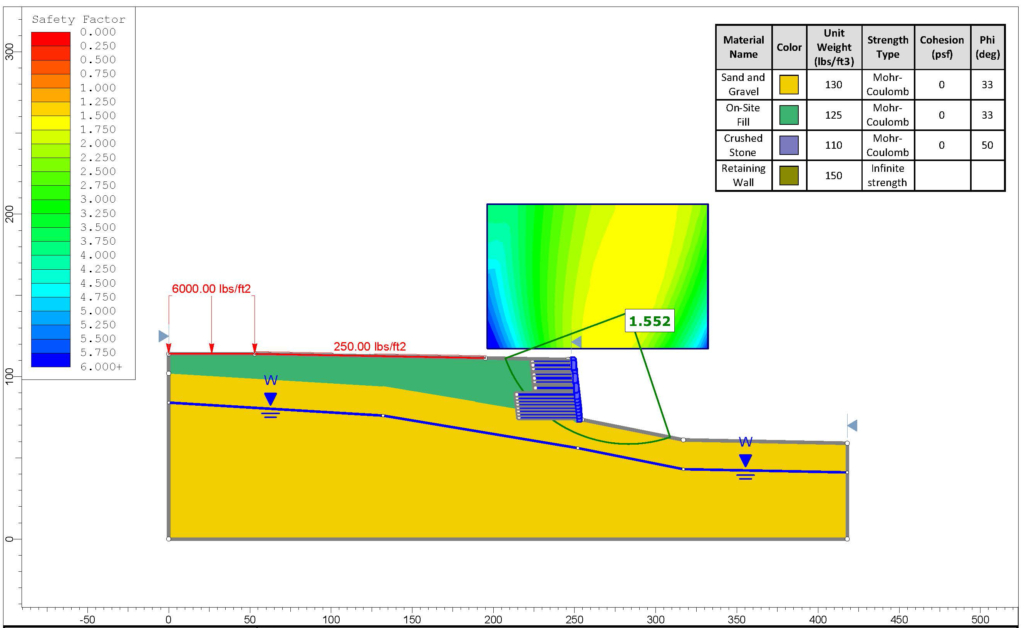
The Geotechnical Engineer’s Role in Tall Retaining Wall Design
Geotechnical engineers play a pivotal role in the successful design of tall retaining walls, especially for high-load commercial applications. Geotechnical engineers work with wall designers to evaluate the overall (global) stability of the site, to determine the potential for hydrostatic pressure to be present behind the wall, and to provide soil parameters for wall design. Key responsibilities of the geotechnical engineer can include:
- Geotechnical subsurface investigations: A thorough geotechnical subsurface exploration program is critical for understanding site soils and how they’re incorporated in retaining wall design. Data from Standard Penetration Tests (SPTs) can be used to correlate engineering properties of the soil (such as unit weight, relative density, and internal angle of friction) which will inform the conceptual design and allow for early problem detection.
- Global stability analysis: The geotechnical engineer should consider global stability analysis for retaining walls (See figure 1 for an example). Software like Slide by Rocscience is a valuable tool for analyzing the global stability of retaining walls under various conditions (i.e., surcharge loading, seismic loading, flood conditions, etc.).
- Assessing lateral pressures: Taller retaining walls face greater lateral earth pressure, particularly when surcharges from heavy warehouse operations are factored in. Geotechnical engineers evaluate these pressures and determine whether specific reinforcement—like additional geogrid, tiebacks, anchors, or counterforts—is required to improve wall performance.
Without precise geotechnical assessments, the risk of retaining wall failure–including sliding, overturning, and settling–significantly increases. Failures could lead to structural damage to the facility, costly repairs, downtime for the warehouse operations, and injury or death.
Regulatory and Compliance Requirements for Retaining Walls in Massachusetts
In Massachusetts, retaining wall projects for commercial buildings must adhere to both state and local regulations, which ensure safety and environmental stewardship. Some of the key standards include:
- Massachusetts Building Codes: Building codes set specific standards for retaining walls, particularly those above certain heights or load capacities, which are common in warehouse applications. Requirements may include engineered designs, stability calculations, and load-bearing analysis.
- Environmental regulations: The Massachusetts Department of Environmental Protection (MassDEP) mandates erosion control and soil stabilization on construction sites, particularly near bodies of water or protected areas. Since retaining walls are often used to maximize usable space, it is not uncommon for the walls to abut critical wetland resource areas.
- Industry standards: Standards such as the American Society of Civil Engineers (ASCE) and the Nation Concrete Masonry Association (NCMA) for segmental retaining walls guide best practices for wall construction, materials, and drainage solutions, enabling high-performance outcomes for tall retaining walls.
Understanding and adhering to all applicable regulations are essential to prevent project delays, avoid fines, and ensure the long-term safety and functionality of the wall.
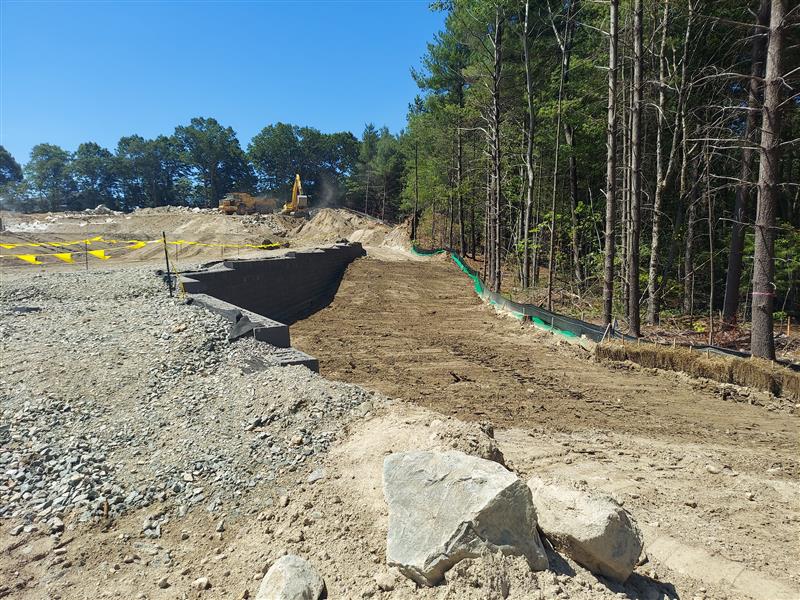
Conclusion: The Strategic Value of Geotechnical Engineering for Retaining Walls in Industrial Settings
Retaining wall design for warehouse and logistics centers is a specialized task that demands a robust understanding of soil mechanics beyond what is typically performed for retaining wall design. Tall retaining walls can support significant large development projects but will require additional geotechnical engineering throughout the design process.
Geotechnical engineers bring essential expertise to the life cycle of retaining wall designs. The goal of the geotechnical engineer is to use their technical knowledge to evaluate retaining walls for safety, durability, and compliance with regulations, ultimately protecting the investment of the developer and the safety of those using the site. Engaging a geotechnical engineer is not just best practice—it’s an essential step in delivering successful, high-performing retaining wall systems for the industrial sector.
Posted In: Articles
Tagged In: Development